Meet The Experts
The SeaKing Group was established in April 2001; specialising in marine electrical engineering. SeaKing’ targets maintenance and project work for commercial ships, ferries, naval vessels, cruise ships and superyachts. The company work across Europe, Asia and the Americas covering many market segments of the marine sector. Over the years SeaKing have so-far employed over 100 apprentices. SeaKing is certified through Bureau Veritas for the ISO9001 and 14001 management standards.
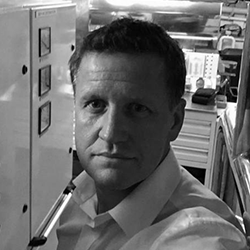
Martin Sealeaf
CEO
Building for the Next Generation
As a result of the digital disruption over the last decade, we have seen the tech industry BOOM, creating new money and younger billionaires! This younger generation comes with more adventurous imaginations requesting extra unusually designed vessels challenging the expectation of the Superyacht industry.
Luxury yachts have been decorating our seas since the beginning of the 20th century. The architecture and engineering have massively evolved, pushing the boundaries, and keeping up with the demands of the next generation owners.
We spoke with Martin Sealeaf, CEO of The SeaKing Group, to find out his thoughts on building Superyachts for the next generation.
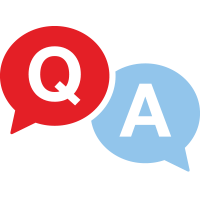
Q1: What changes within the superyacht sector have you seen in the last decade?
A: Over the years, we have seen the prolific capability of engineers to meet the satisfaction of the owner’s, capturing their imagination, desires and scientific endeavours. There is a great emphasis to embrace every aspect of technology to enable the vessel to become a citadel for owners. During the design phase, consideration is needed to empower owners to stay connected onboard, so business affairs become seamless while maintaining a vein of fun that is required of the circles that the owners must immerse themselves.
Vessels are now travelling further, and more frequently changing their destinations, and as an engineer, you are highly reliance on being self-
supportive; with a go-anywhere attitude rather than being tied to a dock.
As technology is evolving, there is now far more dependence on power availability and quality to cope with more sophisticated power trains such as POD propulsion and stabiliser systems. There is an increasingly high trend in video walls and floors with elevated demands on processing power for IT systems. Other requests within designs of vessels include innovative static systems combined with Hybrid solutions.
Q2: How have the designs of ‘explorer yachts’ evolved?
A:The capability for yachts to explore further and in more extreme conditions while looking sleeker is becoming increasingly popular.
The design and engineering efforts are being put into building stronger vessels. For example, ice-class hull being incorporated into a design while maintaining the palace-like status.
Q3: Thinking about the Next Generation of owners, what do you think will be the next trend?
A: Opulence will continue, and with that will come; more elaborate online stay connected systems and automation of processes.
The industry will also see more significant design challenges to incorporate the following;
• Gyro stabilised entertainment systems
• Noise reduction (hybrid)
• Closer to the water designs and glass decks
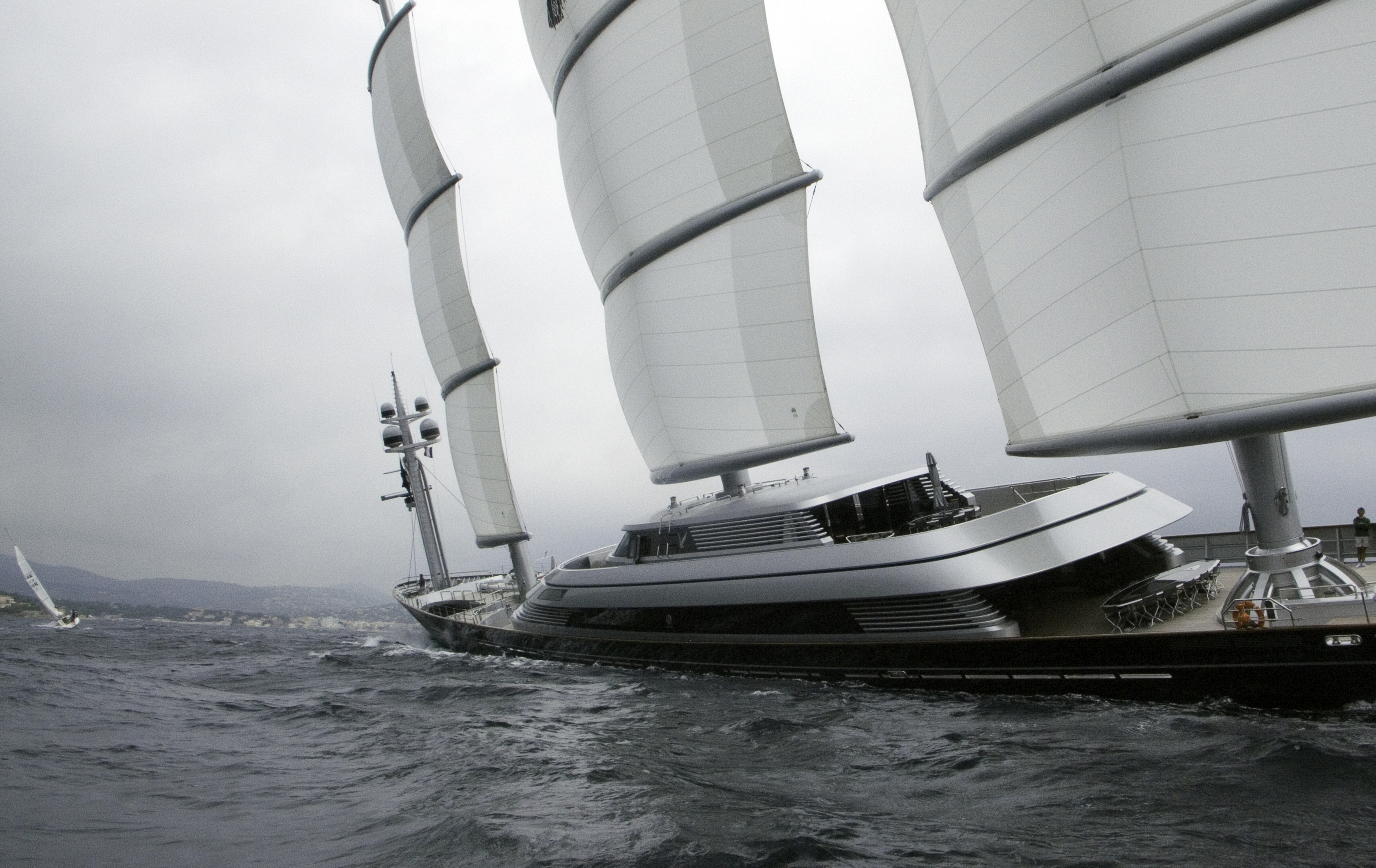
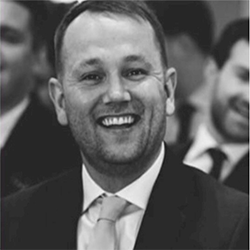
Blaise Cockton
Marine Engineer
A Deep Dive into the journey of a Marine Engineer Apprentice
The SeaKing Group to this date has now proudly employed over 60 apprentices. The leading marine electrical specialist currently employs more than 100 engineers worldwide with a track record delivering projects across Europe, Asia, Africa, the Middle East, Caribbean and USA.
Marine Engineers are responsible in the industry for installing, maintaining, fault finding and repairing marine engines, ancillary systems and equipment on marine craft including yachts, workboats, cruise ships and superyachts.
SeaKing Group’s CEO Martin Sealeaf said ‘Apprenticeships represent a long-term investment for the group, the candidates undergo rigorous panel interviews before securing their roles. SeaKing invests heavily in such schemes because they provide an excellent foundation in technical skill and knowledge. We can then steer the recruits into world-class marine electrical engineers.’
We spoke with Blaise Cockton has been with SeaKing for over 13 years starting off his career as an apprentice, we had a chat with Blaise to find out about his
experience.
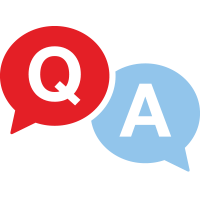
Q1: Tell us how the opportunity of being an apprentice for The SeaKing Group came up?
A: I was a student at TTE Engineering College in Ellesmere Port where the college put forward a number of appropriate candidates to interview with SeaKing and I was a successful applicant. I was then sponsored through 12 months of full-time college before joining The SeaKing Group as a full time employee in September 2008.
Q2: Talk us through the various positions you’ve so far held at the SeaKing Group
A: 2008 – 2011 – I served the remainder of my technical apprenticeship program, learning on the job whilst attending college on day release.
2012 – I joined the organisation technical design/support office as technical draftsman, a position that naturally evolved into design engineer, followed project engineering role, through broad experience and extensive training/qualifications.
Tasks included the use of software packages; AutoCad for drawing production and Etap for power systems calculations and analysis, as-well
as nationwide and overseas ships surveys for specification production, technical equipment selection and procurement, control system design and the management of global freight forwarding of equipment required for works.
2017 – present – I am now a project manager, taking control and ownership of all aspects of projects from start up to closure.
Q3: What tasks does your current job involve?
A: At the current stage of the project ahead of the imminent arrival of Type 45 Destroyer ship – one of six, required tasks include finalising and verifying designs, completing work packages, highlighting and endorsing variations to agreed scope and designs, planning for embodiment, highlighting and mitigating project and programme risks, and reporting on progress and issues to the board.
Q4: What do you like most about your current position?
A: Project diversity, every project offers different challenges daily. Also, my current opportunity to be so heavily involved in such a fantastic project working on the detailed design and its delivery of an MoD’s Type 45 Destroyer Power Improvement Project for the Royal Navy, implementing the resilience and operational capabilities of one of the most advanced warships in the world.
Q5: Are you given a variety of projects to manage?
A: A wide variety. Some recent projects include a redesign and subsequent retrofit of an autonomous power management system on-board a superyacht in Italy, to a wheelhouse console design, installation, and navigation and communication system integration on board a new build RO-RO passenger ferry and, of course currently the Royal Navy Type 45 Destroyer Power Improvement Project.
Q6: What kinds of challenges are you faced with while on the job?
A: Several types of challenges dependent on the project, whether it be technical complexities during design, fast moving time constraints during production or varied stakeholder management – all good fun!
Q7: Do you have any tips or advice on becoming a Project Manager within Marine Engineering?
A: Hard work and dedication with an agile approach to each day in work.
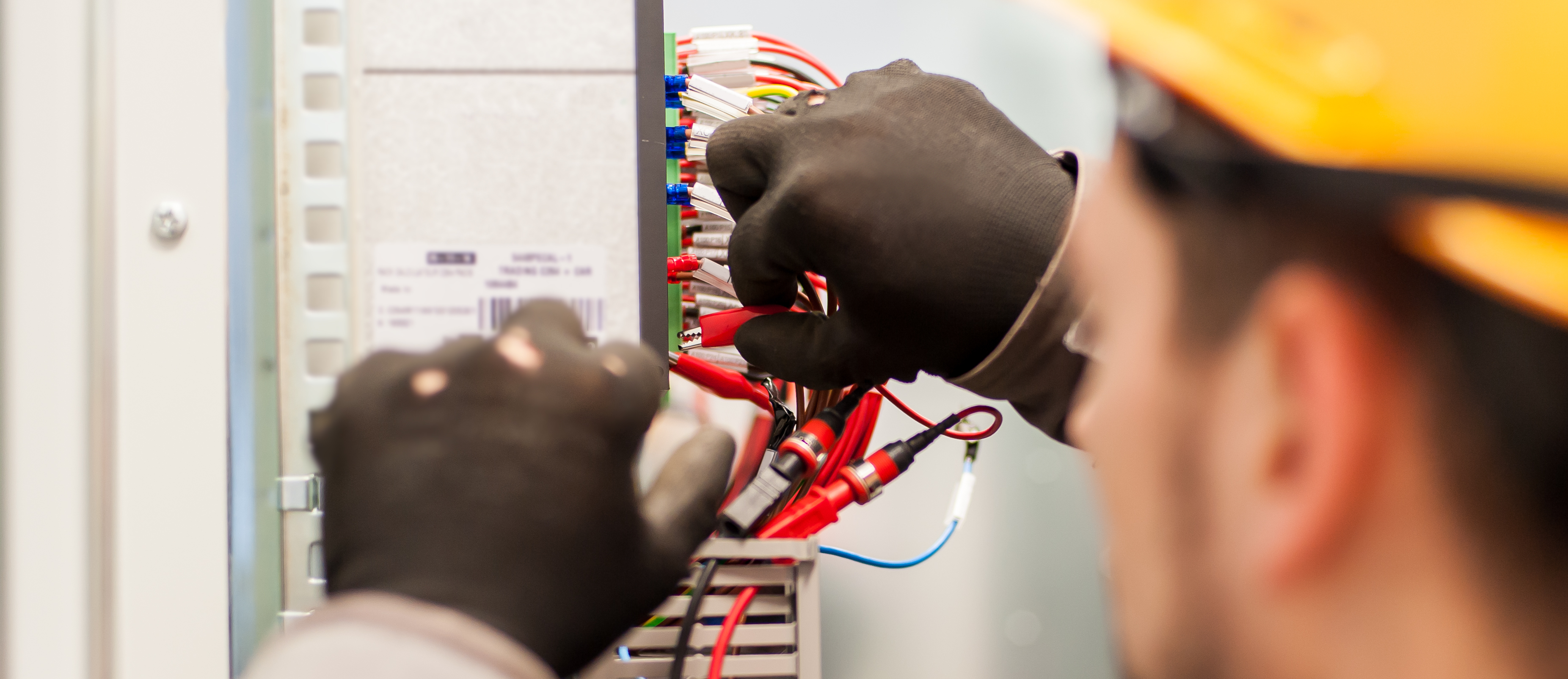
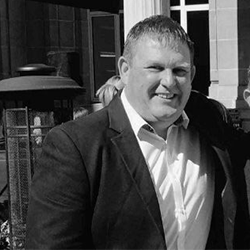
Gary Pink
Design Manager
Successful ONBOARDING: Transferring military skills to civvy street
After a successful career in the Royal Navy as a Weapons Engineer, it was time for our Design Manager Gary Pink to pack his service bag for the last time and hang up his boots.
We took some time to find out about Gary’s experience settling into civilian life.
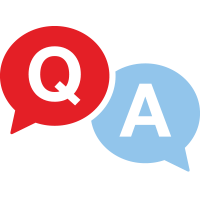
Q1: Tell us about your service career
A: I joined the Royal Navy in 1986 and served for 22 years; leaving the service in 2008. I was on several vessels including HMS York, Leeds Castle, Dumbarton Castle, Liverpool, Southampton, and Albion. I also had several drafts (what we called appointments) to Shore Bases including HMS Inskip, Forest Moor, RN Gibraltar (where my wife and children accompanied me) and RAF Henlow. I was a Weapons Engineer however that does not mean that I worked on weapons all the time. Most of my time was working on either RADAR or communications systems. I learnt my trade (Electrical Engineering) at the Naval Engineering Establishment HMS Collingwood. I worked my way through the ranks eventually finishing off as a Chief Petty Officer; I like to think that I had a successful career culminating in me receiving the Meritorious Service Medal (MSM).
Q2: How did the opportunity as Design Manager for SeaKing Group come about?
A: It came about by chance really. I was originally employed to be part of a service team however, I was put on the ‘tools’ on a couple of the RFA vessels; to see how things worked with the company then one day I was asked to go to the main office. I was told that the specification writing was increasing, and they needed someone to do it; I was asked, and I accepted. As time progressed, and as other projects came in, I started taking things on to help in the RFA side of things. As the team (Design) started to build we were moved up to our current office. I was asked to keep an eye on what was occurring in the office to see that things were ok. It kind of moved on from there and eventually I was made manager of the team – we are hoping in the future to be able to provide full turn-key packages, from the office to our future clients.
Q3: What do you miss about being in the Navy?
A: If you ask anybody, they will say the lads – they do not miss the job but the lads – this is quite true. Although I am very proud of my service the craic and the banter are what is missed; and whenever we meet up with old friends it just like we saw them yesterday.
Q4: What do you like most about your current position?
A: Although at times the job can be stressful no two days are the same, and every day we seem to learn something new. I also like being able to pass on some of my knowledge, as well as learning from, some of the younger ones who have not long been in the office. I also like it when I see people who have worked in the office move onto other positions within the business.
There are many known attributes that are identified as essential skills needed in the military. Including leadership, teamwork, communication.
Q5: What skills have you transferred over to your current role?
A: Well there is my engineering background of course, and my knowledge of military vessels and the ‘language’ that ships staff talk (I was told it was one of the reasons as to why I was asked to write the specifications).
You have also mentioned it in the question – teamwork, leadership and communication – all of which was taught to me as I progressed through my career.
Q6: Do you have any tips or advice on a smooth transition to other service leavers?
A: Never sell yourself short and have the courage of your convictions. All the skills that you have obtained are fully transferable. Although it may feel strange when you first leave, civvy street is not all that bad and there are plenty of ex-service personnel out there to help you if required; its always good to talk (and it helps).
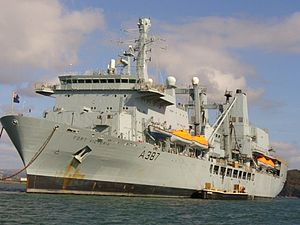
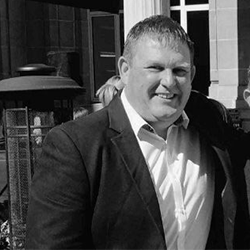
Gary Parsons
Procurement Manager
Challenges of a sustainable procurement strategy; Promoting the importance of a dependable supply-chain
Sustainable procurement demands strong collaboration and engagement between all businesse’s within a supply chain. The ideal of a sustainable procurement achieves a systemic value-add promoting positive outcomes for the company, the economy, environment, and society.
We spoke to Garry Parson Head of Procurement for SeaKing, to grasp an insight into his role. Finding out about some of the tools and techniques their business has adopted-to support sustainable procurement.
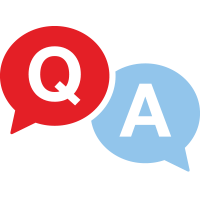
Q1: Tell us about your journey so far with SeaKing
A: I joined the team at SeaKing back in March 2018. I was approached by one of the directors when working for a local wholesaler in a similar role and had a previous supplier/client relationship with SeaKing. There is a small team in the department including two others that work with me supporting the procurement process.
Q2: What does a day in your role at SeaKing look like?
A: My working day is always very busy at SeaKing – which I like! I work closely with the wider team of engineers at SeaKing of around 20 individuals. Due to the nature of our business much of my work can be quite reactive, with tight deadlines to adhere to. The marine industry is quite unpredictable with regards to meeting demands of breakdowns; the vessel will need the equipment to enable sailing, so the turnaround needs to be very quick. We also have ongoing maintenance contracts which we purchase for and this gives us the opportunity to build up great relationships with suppliers and ensure we obtain the best price for the project which reflects in the price we give to our client. My role within the department includes leading negotiations with suppliers to ensure cost effective supply solutions are obtained.
Q3: Maintaining and building business relationships with suppliers are an importance for your role, how do you achieve this?
A: Every day I keep my communication ongoing with suppliers and stakeholders. I ensure that I make suppliers aware of new projects and identify opportunities to improve equipment and service costs. Our regular suppliers receive continuity of business, which reflects in the rate they give us as a loyal customer.
Q4: How do you manage complex project environments at SeaKing?
A: The engineering team I work with at SeaKing – I know well and understanding how the individuals work is really important and helpful to my role. We have multiple projects happening simultaneously all with various deadlines, complexities, and challenges. When I get the opportunity, I try to grasp a good understanding of the project this supports me to plan the procurement and keep to deadlines.
Q5: SeaKing have built relationships over the years with local suppliers – how important is this to the business?
A: We are always very considerate of working with local suppliers and try to be environmentally sustainable where we can. As an established business of 20 years we are conscious about contributing to the local economy. However, as a department we also need to be aware of budgets and timeframes. Purchasing directly from the source which may not be local – can occasionally reduce costs to us and the client and of course promotes reduction of emissions.
Q6: What is the biggest procurement challenge in marine engineering that you are facing?
A: The two challenges that come to mind are time pressures and keeping on track with complex projects. Sourcing of complex parts is essential to our business. The technical specifications for these components are commonly managed by external suppliers, which can cause time delays and unpredictability.
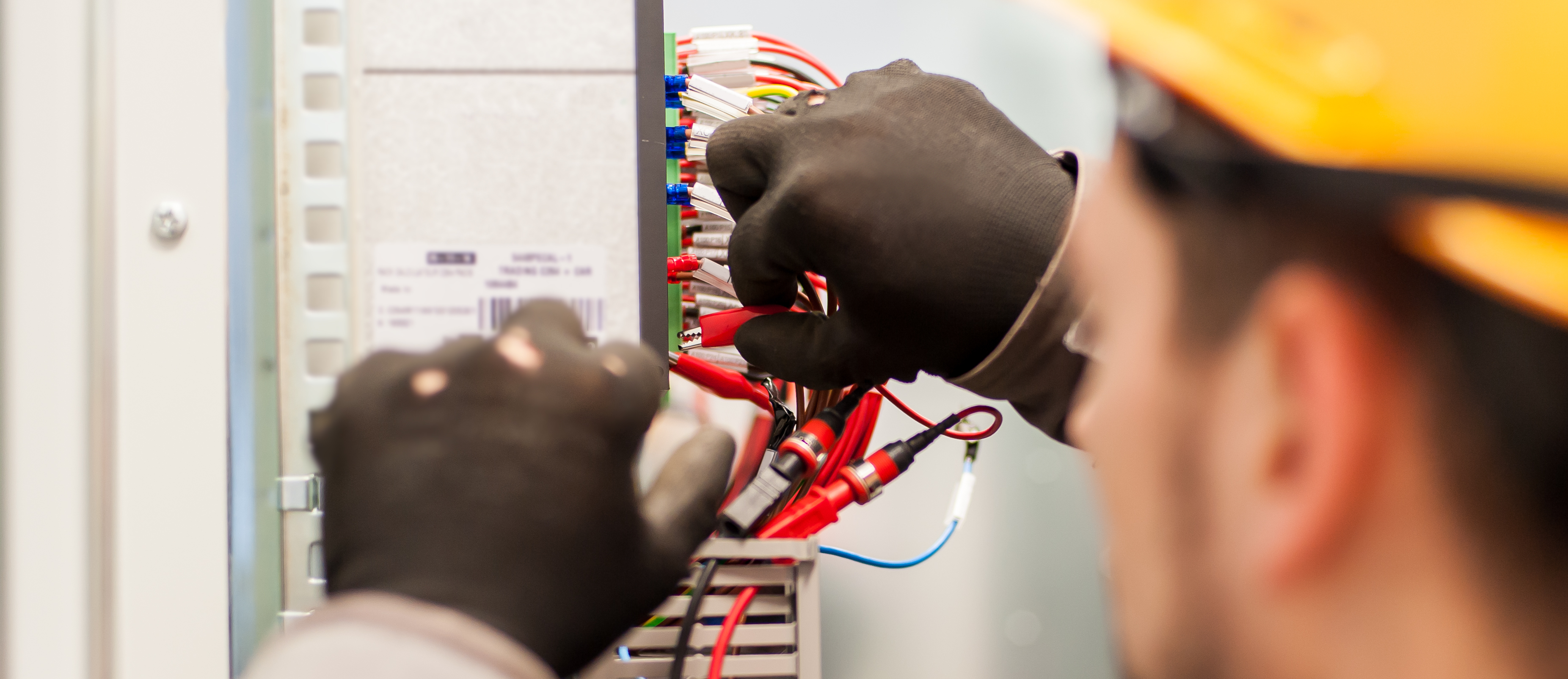